Schäfer – Menk: How Aiviro Robot Streamlined Company Processes
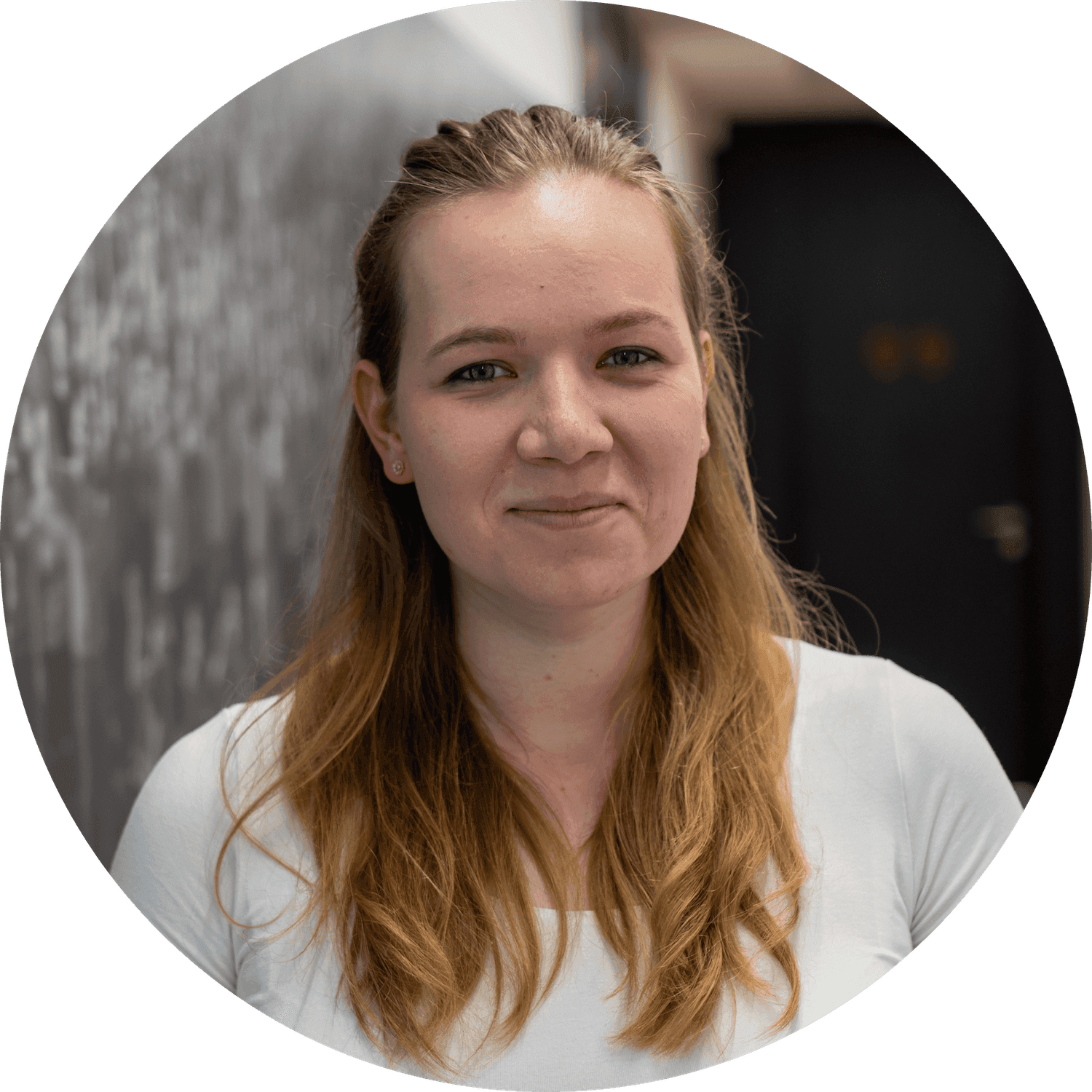
Kateřina Stoklásková
Oct 03, 2024 • 4 min read
An an interview with Ing. Ctirad Hájek, IT Manager at Schäfer-Menk, we discussed their experience with the Aiviro Robot. The company, which manufactures welded assemblies for mobile cranes, simplified time-consuming tasks like checking steel sheet certifications thanks to Aiviro Robot. Mr. Hájek explains how automation saved time and improved the overall functioning of their processes
Could you briefly introduce your company and describe the main activities you focus on?
Our company, Schäfer-Menk, manufactures welded assemblies for mobile cranes, transportation, and storage equipment. We have over 500 employees and operate two plants – in Prague-Radotín and Dýšina near Plzeň. Our customers are the world’s and Europe’s leading mobile crane manufacturers, such as Liebherr.
What routine tasks did your company face before implementing the Aiviro Robot, and what prompted you to try it?
One of the main reasons was that we use the Helios system and also have strict rules for manufacturing, inspecting, and tracing products for mobile cranes. This may seem like a simple task, but for example, receiving steel sheets is a very time-consuming and critically important activity. Therefore, we must be able to trace what material was used to produce each part.
What I consider the most important is not just implementing the Robot to perform the task, but mainly improving our company processes.
What specific task does the Robot handle for you?
Our first task or scenario for the Robot is receiving steel sheets and checking their certifications. This means verifying the composition of a specific batch— the proportion of certain elements listed in the foundry’s report.
The Robot checks the certification against the standard prescribed by the customer. In the event of a defect, we cannot accept the steel sheet. If everything is in order, we can proceed with receiving it. We also need a system for the serial numbers of each steel sheet so that we can trace what material we are using during production. It’s a very complex task.
When we started over a year ago, we didn’t expect it to be so complex. We found that the process was sometimes cyclical, with various dead ends, etc. What I consider the most important is not just implementing the Robot to perform the task, but mainly improving our company processes.
Now we have a database where we can easily find what our customer needs, even from four years ago.
How much time does Aiviro save you on a single task, for example, when receiving steel sheets?
The savings we estimated are approximately 100 working hours per month. It may seem like a small amount, but it’s an unpleasant and highly important task.
Today, quality work is not just about saving time but also about having better-organized certifications and even a historical archive of them. We used Aiviro Robot to digitize our old data. Now we have a database where we can easily find what our customer needs, even from four years ago.
How many tasks is the Robot currently handling? Do you plan to expand the Robot’s role?
We currently have eight scenarios, but we want to use the Robot more. That’s why we took another step and expanded our team with a qualified colleague who can program the Robot. This person also has, with our support, the ability to understand our company processes. This isn’t a given. Many people we meet in the company don’t perceive what they’re doing as a process that is part of the main process – production and delivery to the customer. They often perform tasks without knowing why.
But the Robot cannot function this way. We don’t want to preserve the current state. We want to improve it, and every process can be improved. For me, the Robot is a tool for improving processes. This means not only automating but mainly making them more efficient.
So by working with the Aiviro Robot, you’ve reviewed processes to eliminate unnecessary tasks.
Not only that. Stable processes improve a company’s business. The company is no longer dependent on whether someone leaves, and you don’t know how things were done. Suddenly, you have a clear process. We have a diagram that outlines how the Robot works. We also discovered that it’s beneficial to create a second diagram that shows how a person works and when interaction between them occurs.
This means that when someone starts working, they have a flowchart of what to do. They know when to call the Robot or how to start it. They know how to respond to what the Robot has processed because the Robot can tell them: “I’m missing this, please provide it.” or, “I successfully processed this, you can check it.”
When the Robot is missing some information, it sends a notification to the employee and says: “Sorry, this standard isn’t in my database, I need it entered.”
Why would you recommend Aiviro to other companies?
Besides the obvious automation, I would emphasize that I don’t know any company where processes couldn’t be improved. Things change and evolve, so what was excellent may become an outdated approach in a few years.
I’m convinced that we always have room for improvement. Aiviro is a great tool because it forces you to think about processes. It makes you dive deep and ask – do we really need to do it this way, or could it be done differently?
Thanks to Aiviro, we created a detailed, structured catalog of steel casting standards for the first time. Until then, we had several binders of documents describing the standards of our different customers. Each one has different requirements and wants a different standard. No one had previously thought to organize it structurally, and within two to three years, our overview of the standards used had become outdated.
When you want to make work easier for the Robot, you prepare the documents in a structured manner and keep them up to date. When the Robot is missing some information, it sends a notification to the employee and says: “Sorry, this standard isn’t in my database, I need it entered.” The employee turns to the quality manager and asks them to add the standard to the system. Then the Robot is restarted, and everything proceeds as it should.
Thank you, Mr. Hájek, for sharing your experience with Aiviro Robot. It’s clear that automation not only saves time but also improves processes.
Want to know how Aiviro Robot can help you? Contact us, and we’ll be happy to show you what it can do.
Kateřina Stoklásková
Marketing